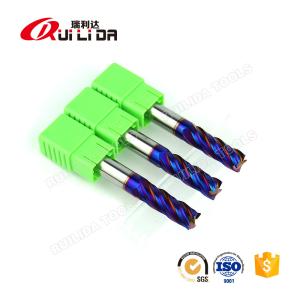
Add to Cart
HRC65 4 Flutes Extra Long Corner Radius End Mill 12R0.5 Corner Radius Milling Cutters
Product name | RLD HRC65 corner radius end mill 12R0.5 |
Size | 12R0.5*36*100*12D*4F |
Suitable for | Steel, titanium, hardened steel, mold steel, etc. |
Machine type | Finish Milling |
Flutes | 4 |
Coating | Bule Nano |
Helix angle | Variable Helix |
Co | 9% |
HRA | 93.5 |
TRS Min(N/mm²) | 4100 |
Tolerance | Within 0/-0.015mm |
Processing machine | ANCA/ |
Carbide Raw Material Introduction
End mill grade | Carbide rod | Grain size | HRA | Application |
HRC50 | YG10X | 0.6μm | 91.8 | Aluminum, iron, low alloy steel, general steel under hardness HRC45 |
HRC55 | WF25 | 0.6μm | 92.2 | Cast Iron, Alloy Steel, General steel under hardness HRC50 |
HRC60 | GU25UF | 0.4μm | 92.5 | Super Alloy Steel, Stainless Steel, Titanium, Inconel, Hardened Steel under hardness HRC55 |
HRC65 | GU092 | 0.2μm | 93.5 | Alloy Steel, Hardened Steel under hardness HRC62 |
Coating Introduction
Coating name | Color | Thickness | Hardness | Friction | The Max ℃ |
AlTiN | Black | 1.5-3 | 3300 | 0.4 | 900 |
AlTiSiN | Copper | 1.5-3 | 3500 | 0.35 | 1000 |
TiAlN | Dark Violet | 1-3 | 3000 | 0.4 | 800 |
Blue Nano | Blue | 2-4 | 3200 | 0.45 | 1000 |
AlCrN | Dark grey | 1.5-3 | 3500 | 0.3 | 1250 |
DLC | Black | 1-3 | 1800 | 0.1 | 350 |
Diamond | Black | 2-12 | 10000 | 0.02-0.1 | 650 |
The coating also can be customized |
RLD Corner Radius End Mill Standard Size HRC65 | ||||
Flute Dia(mm) | Overall Length(mm) | Cutting Length(mm) | Shank Dia(mm) | Flutes |
2 (R0.2, 0.5) | 50 | 5 | 4 | 4 |
3 (R0.2, 0.5) | 50 | 8 | 4 | 4 |
4 (R0.2, 0.5) | 50 | 10 | 4 | 4 |
4 (R0.2, 0.5) | 75 | 12 | 4 | 4 |
4 (R0.2, 0.5) | 100 | 16 | 4 | 4 |
5 (R0.5,1) | 50 | 13 | 6 | 4 |
6 (R0.5,1) | 50 | 15 | 6 | 4 |
6 (R0.5,1) | 75 | 18 | 6 | 4 |
6 (R0.5,1) | 100 | 24 | 6 | 4 |
8 (R0.5,1) | 60 | 20 | 8 | 4 |
8 (R0.5,1) | 75 | 24 | 8 | 4 |
8(R0.5,1) | 100 | 32 | 8 | 4 |
10 (R0.5,1) | 75 | 25 | 10 | 4 |
10 (R0.5,1) | 100 | 30 | 10 | 4 |
12 (R0.5,1) | 75 | 30 | 12 | 4 |
12 (R0.5,1) | 100 | 36 | 12 | 4 |
Common Milling Problems and Solutions
Excessive Chatter: Vibration and sound are excessive when the tool engages the workpiece.
Possible Solutions:
Increase your feed
Reduce your cutting forces by reducing speed and/or feed or axial and/or radial depth of cut
Increase your system′s rigidity by changing over to a stub length end mill or improving your workpiece fixturing
Change geometry - use an end mill with variable flute spacing or a small circular margin
Poor surface finish
Surface Finish: Work surface looks uneven and feels rough.
Possible Solutions:
Increase system rigidity
Increase speed
Reduce feed
Change to higher helix geometry
Change to an end mill with more flutes
Excessive Wear of End Mill
Excessive Wear of End Mill: Tool is wearing at cutting edges causing poor performance.
Possible Solutions:
Reduce Speed - A 50% reduction in speed will almost double the tool life
Increase/decrease feed - A feed rate that is too light will cause excess rubbing
Change geometry of the tool - Number of flutes, helix angle, length of cut
Change material grade and/or add a coating.